What good is the Eiffel Tower in the middle of your refinery?
Wednesday October 5, 2016
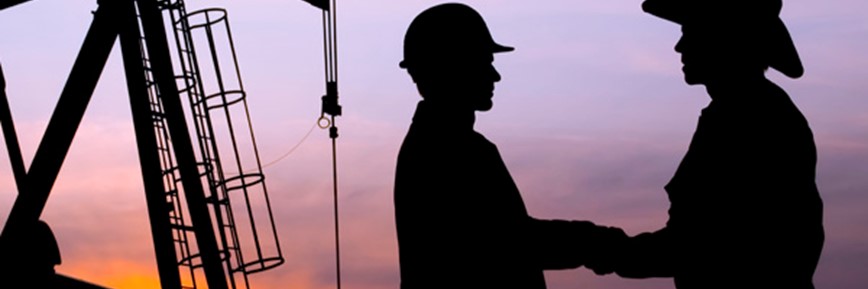
One of the best ways to make sure the design of your refinery is going to look and perform the way you think it should is to perform front end engineering design (FEED) dynamic simulation studies. This truly necessary phase of simulation modeling may save you from building a flare taller than the Eiffel Tower in the middle of your refinery. Don’t laugh – it almost happened.

Oil Refinery at Sunset/Corbis
Dynamic simulation is often only considered for controls checkout and for operator training. However, there are great benefits to be realized by applying dynamic simulation early on in the process lifecycle. For example, conventional methods of flare sizing are conservative in nature but conservative assumptions often lead to unnecessary overdesign, such as calculating that the flare must be as tall as the Eiffel Tower. First principles rigorous simulation helped an engineering company correctly size the flare for all anticipated scenarios and trim 20 million euros off the capital expenditure.
A dynamic simulation model can be developed along with the plant design and evolve throughout the project execution. This saves money at every stage of the process lifecycle from design on through to operations. This is much better than designing and then crossing your fingers in hopes that the plant performs as intended. The benefits and savings from performing a dynamic simulation study early on during the design, before capital expenditure is committed, can be substantial. The model used during the design phase then becomes an asset that grows and can be reused later for further benefits at a relatively insignificant cost.
This blog is the first of a five-part blog series will begin to enumerate the benefits of Dynamic Simulation applied throughout the process lifecycle.
Let’s start with the fi...